The Importance and Application of Die-Casting Parts for New Energy Vehicle Radiators
- Share
- Issue Time
- Dec 21,2024
Summary
In the thermal management system of new energy vehicles, radiators play a vital role, and their die-casting parts are one of the key factors ensuring the performance and reliability of the radiators.
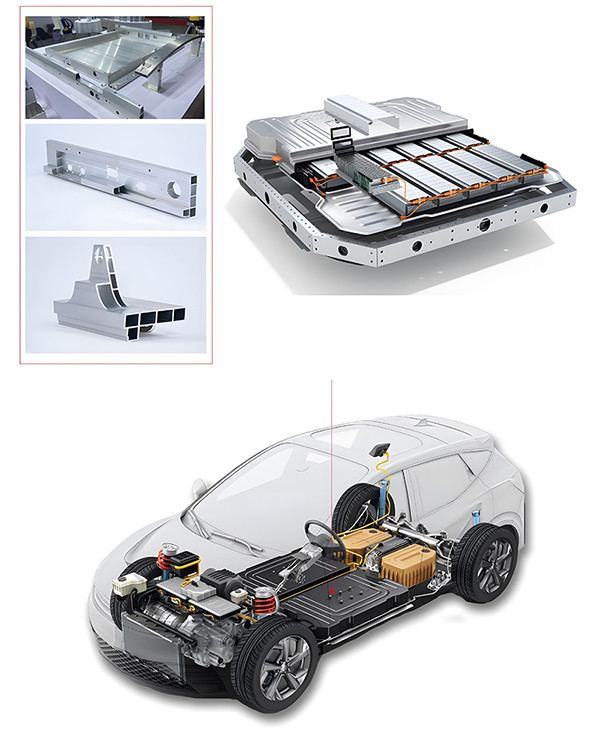
The Importance and Application of Die-Casting Parts for New Energy Vehicle Radiators
In the thermal management system of new energy vehicles, radiators play a vital role, and their die-casting parts are one of the key factors ensuring the performance and reliability of the radiators. With the rapid development of the new energy vehicle industry, the requirements for die-casting parts of radiators are becoming increasingly higher.
Common Materials for Die-Casting Parts
Aluminum Alloy: It is one of the most commonly used materials for die-casting parts of new energy vehicle radiators. It has the advantages of low density, high strength, good thermal conductivity and strong processability. It can meet the demand for vehicle lightweighting while ensuring the heat dissipation effect of the radiator, thus improving the driving range of new energy vehicles. For example, common aluminum alloy grades such as ADC12 and A380 are widely used in manufacturing parts such as the housing and fins of the radiator.
Magnesium Alloy: Magnesium alloy has a lower density than aluminum alloy, higher specific strength and specific stiffness, and also has relatively excellent heat dissipation performance. It is of great significance for weight reduction and heat dissipation optimization of new energy vehicles. Its application in radiator parts, such as in some small radiator components of high-end new energy vehicles or in areas where weight requirements are extremely stringent, can further improve the energy efficiency and performance of the vehicle.
Zinc Alloy: Zinc alloy has good fluidity and casting properties, enabling the manufacture of die-casting parts with complex shapes and high precision. Although it has a relatively high density, zinc alloy die-casting parts can still play their unique advantages in some specific radiator structures, such as certain local connection parts or areas with high requirements for corrosion resistance.
Copper Alloy: Copper alloy has excellent thermal conductivity and relatively high strength. However, its high density and high cost limit its wide application in new energy vehicle radiators. Nevertheless, in some special parts with extremely high heat dissipation requirements and harsh working environments, such as the radiators of high-power motors in high-performance sports cars, copper alloy die-casting parts may be adopted to ensure effective heat transfer and the stable operation of the system.
Main Types of Die-Casting Parts
Radiator Housing: As the outer shell of the radiator, its main function is to accommodate and protect the internal heat dissipation structure and coolant. The die-casting process can produce a radiator housing with a solid structure and good sealing performance, ensuring the normal circulation of the coolant inside and preventing leakage. Meanwhile, the surface of the housing can also be designed with heat dissipation fins or channels to increase the heat dissipation area and improve the heat dissipation efficiency.
Heat Dissipation Fins: They are the parts that directly contact the air for heat exchange in the radiator. Heat dissipation fins produced by the die-casting process have thin and uniform wall thicknesses, precise shapes and sizes, and can be closely arranged on the surface or inside of the radiator housing to form efficient heat dissipation channels. The shapes and structural designs of heat dissipation fins are diverse, with common ones including parallel plate-shaped, corrugated and pin-shaped ones. Different shapes are suitable for different heat dissipation requirements and airflow environments.
Water Pipe Connectors: They are used to connect the radiator with the cooling water pipeline to ensure the smooth inflow and outflow of the coolant. Die-casted water pipe connectors have good sealing performance and mechanical strength, can withstand certain pressures and vibrations, and prevent coolant leakage. Their interiors are usually designed with precise flow channels and sealing structures to ensure the uniform distribution and efficient circulation of the coolant.
Fan Mounts: Fans are an important part of the radiator's heat dissipation system, and fan mounts are used to fix and support the fans. Die-casted fan mounts have high rigidity and stability, which can ensure the installation accuracy and reliability of the fans when they are running at high speeds, reduce vibration and noise, and thus improve the performance of the entire heat dissipation system.
The Impact of the Die-Casting Process on Part Quality
Dimensional Accuracy: Advanced die-casting processes can ensure that die-casting parts have high dimensional accuracy, thus ensuring good fit between various parts. For example, the precise fit between the radiator housing and parts such as heat dissipation fins and water pipe connectors can effectively reduce the risk of coolant leakage and improve the overall performance and reliability of the radiator.
Surface Quality: The design of molds and the control of process parameters during the die-casting process have an important impact on the surface quality of the parts. Good surface quality can not only improve the appearance quality of the radiator but also enhance its corrosion resistance and extend its service life. By optimizing the die-casting process, defects such as pores, shrinkage cavities and cracks on the surface of castings can be reduced, making the surface of the parts smoother and flatter.
Internal Structure: The die-casting process enables alloy materials to solidify rapidly under high pressure, forming a fine and uniform internal structure, thereby improving the mechanical properties and fatigue resistance of the parts. For new energy vehicle radiators, this means that die-casting parts can better withstand vibrations, impacts and thermal stresses during vehicle driving, ensuring the stability and reliability of the radiator during long-term use.
Industry Development Trends
Integrated Die-Casting: With the continuous increase in the requirements of new energy vehicles for production efficiency and cost control, the application of integrated die-casting technology in the manufacturing of radiator die-casting parts has gradually attracted attention. Through integrated die-casting, multiple radiator parts can be integrated into one large die-casting part, reducing the number of parts and assembly processes, improving production efficiency, reducing production costs, and also enhancing the overall structural strength of the radiator.
Research and Development of High-Performance Materials: In order to meet the needs of new energy vehicles for higher heat dissipation performance and lightweighting, the research and development of new high-performance die-casting materials has become an important direction for industry development. For example, developing aluminum or magnesium alloys with higher thermal conductivity and lower density, and improving the comprehensive performance of materials by adding special elements or adopting new preparation processes will provide strong support for the upgrading of die-casting parts for new energy vehicle radiators.
Intelligent Manufacturing and Quality Control: With the help of advanced intelligent manufacturing technologies, such as automated die-casting production lines, online inspection equipment, and big data analysis, the intelligent production process and precise quality control of radiator die-casting parts can be realized. Through real-time monitoring and data analysis, die-casting process parameters can be adjusted in a timely manner, the production process can be optimized, the consistency and stability of product quality can be improved, the rejection rate can be reduced, and the market competitiveness of enterprises can be enhanced.
Die-casting parts for new energy vehicle radiators play an indispensable role in the vehicle's thermal management system. With the continuous progress of materials science, die-casting processes and manufacturing technologies, die-casting parts for radiators will develop in the directions of high performance, lightweighting, integration and intelligence, providing more reliable guarantees for the efficient operation and sustainable development of new energy vehicles.